The standard of uncooked supplies getting into the manufacturing facility has a direct impression on the standard of the completed merchandise, making efficient provider high quality vital for manufacturing success. Being part of the bigger image of Whole High quality Administration (TQM), which encompasses adherence to specs, design high quality, course of high quality, and supply high quality, provider high quality is the place all of it begins. Nonetheless, as a result of shortages, logistical disruptions, and rising prices, sustaining materials high quality has change into more and more troublesome.
In keeping with Aberdeen’s analysis, the rising value of uncooked supplies is the highest operational problem producers face in 2023, together with the complexity of world provider networks. On this article, we’ll have a look at how Finest-in-Class producers handle supply chain high quality and current methods for prioritizing provider relationships and planning successfully amidst disruptions.
For this reason provider high quality is so vital for producers.
Operational Challenges Affecting High quality Administration Processes in 2023
Aberdeen’s analysis reveals the highest operational challenges producers face with their quality management processes:
- Rising value of uncooked supplies – 36%
- Growing product complexity – 30%
- Complexity of world provider networks – 25%
- Lack of coaching for high quality assurance – 23%
- Frequent design adjustments – 23%
Inflation, worker turnover, and power prices are the principle culprits of the rising value of uncooked supplies. With fewer staff to generate and transport supplies and elevated value of doing enterprise, working prices for suppliers are by way of the roof, inflicting suppliers to extend costs simply to remain within the black. Plus, the identical quantity of demand for much less available provide permits suppliers to drive up costs. Vitality prices and insurance policies round power consumption are growing transportation prices, contributing to larger value factors.
Product complexity can also be a difficulty for producers. Because the tempo of innovation continues to speed up, prospects are demanding extra options and capabilities for his or her merchandise. Producers should be able to shortly herald new suppliers to fulfill time-to-market targets for brand spanking new product introductions (NPIs). The necessity to develop relationships with suppliers as buyer wants and enterprise methods shift will increase the complexity of world provider networks. Visibility into provider high quality is necessary for producers trying to cut costs and enhance product high quality.
Finest-in-Class Methods for Addressing Provide Chain Pressures
So, the query turns into: what can producers do to beat these provide chain challenges and successfully predict scheduling, value, and high quality for uncooked supplies? how Finest-in-Class corporations are dealing with provide chain high quality reveals viable options.
Aberdeen defines Finest-in-Class producers as the highest 20% of companies based mostly on their self-reported efficiency in key high quality metrics, together with the % of merchandise assembly high quality targets, % of merchandise shipped with zero defects, value of non-quality (recollects, guarantee, and so on.), and buyer satisfaction. These top-performing organizations are extra prone to observe and leverage quality data to help provider high quality administration.
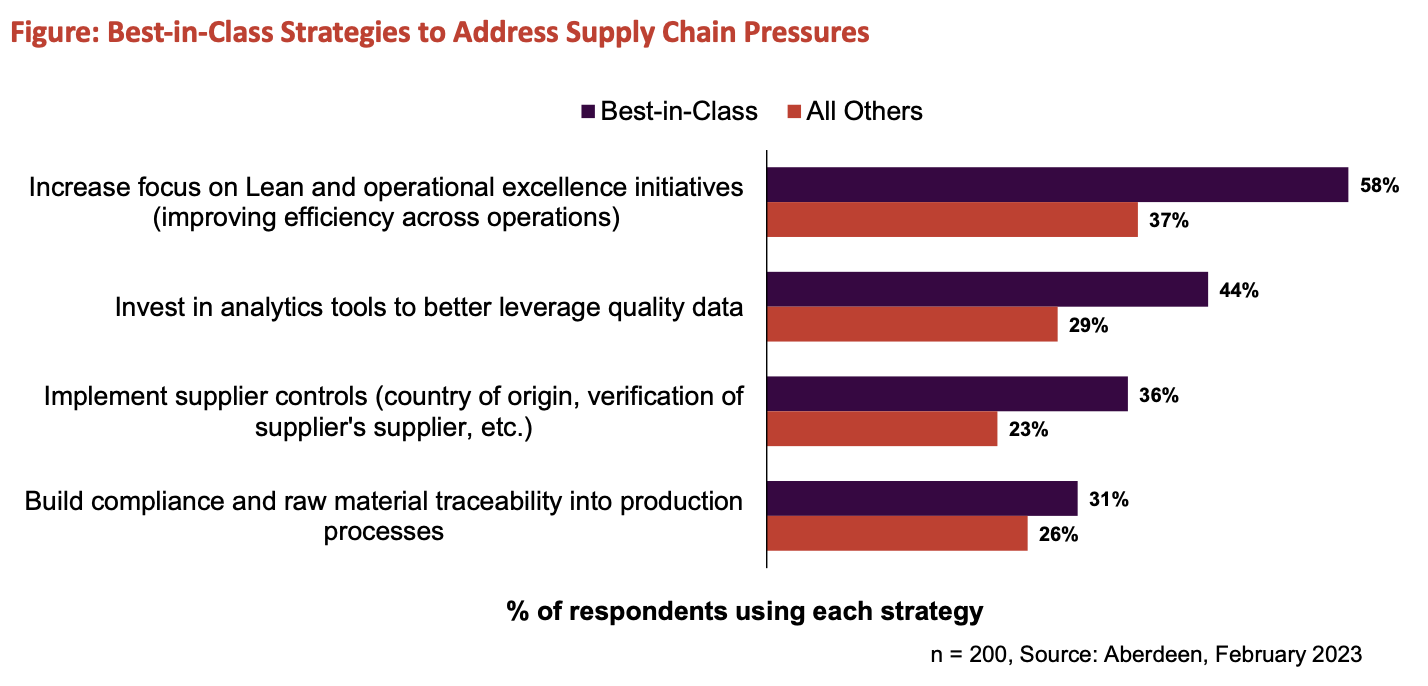
Determine: Finest-in-Class Methods to Handle Provide Chain Pressures
1. Concentrate on Lean Manufacturing
Finest-in-Class corporations usually tend to give attention to Lean manufacturing initiatives to scale back the quantity of uncooked supplies in stock to help manufacturing. This entails slicing down on bodily prototypes, design adjustments and ECOs, the house, motion, and operations for accessible stock, and materials waste wherever potential. With end-to-end options like PLM to observe and optimize uncooked materials utilization and traceability, Finest-in-Class corporations can in the reduction of on spending and working prices.
2. Construct Compliance and Traceability into the Manufacturing Processes
To allow Lean manufacturing methods, the Finest-in-Class construct compliance and uncooked materials traceability into manufacturing processes to successfully observe and measure utilization. Government visibility into these metrics by way of dashboards and centralized databases permits enterprise leaders to match efficiency in opposition to targets and alter as wanted to attain their Lean manufacturing targets.
3. Put money into Analytics
Finest-in-Class producers additionally put money into analytics to tie materials high quality again to suppliers. This permits them to prioritize relationships with suppliers who’ve traditionally offered top quality supplies and cease working with those that don’t. Visibility into provider high quality on the enterprise degree permits completely different groups and website places to align provider choices with these insights. Provider controls assist to make sure standardization of provider choices throughout the corporate.
Advantages of Finest-in-Class Methods
These capabilities assist the Finest-in-Class plan and execute even throughout instances of financial uncertainty. On common, Finest-in-Class corporations expertise…
-
Better uncooked materials high quality – 48% extra materials tons/shipments/batches accepted inside tolerance.
- Finest-in-Class Avg: 74%
- All Others Avg: 50%
-
Higher relationships with suppliers – 44% extra licensed suppliers (their information is trusted for inspection outcomes).
- Finest-in-Class Avg: 75%
- All Others Avg: 52%
-
Quicker time-to-market – 47% extra full and on-time outbound shipments.
- Finest-in-Class Avg: 72%
- All Others Avg: 49%
*Benchmark your group’s efficiency in opposition to the Finest-in-Class numbers above to see what adjustments you’ll want to make to attain Finest-in-Class efficiency.
Begin Implementing These Methods Right this moment
To summarize the significance of provider high quality for producers, contemplate the frequent phrase: “The entire is bigger than the sum of its elements”, that means the work carried out collectively is healthier high quality than the aggregated work of particular person parts. However the high quality of the elements is crucial to the standard of the entire. If one half doesn’t pull its weight, your entire group can fail. That’s why leaders at Finest-in-Class corporations convey the suitable supplies into their factories on the proper time.
Closed-loop materials quality management processes, enabled by traceability and analytics, permit Finest-in-Class producers to relay the defect and efficiency rankings of shipments again to procurement groups to optimize provider choice. They will then construct relationships with suppliers which are probably the most dependable and value efficient, boosting their batch acceptance charges and share of licensed suppliers. Additionally they prioritize Lean manufacturing to scale back the quantity of uncooked supplies to help their manufacturing wants, leading to better reductions in waste and working prices.
Implementing these methods can in the end assist any producer get high-quality merchandise out the door shortly with minimal change orders and defects, which ends up in fewer recollects and guarantee claims. By reaching time-to-market targets and maintaining prospects happy, manufactures can set themselves up for steady operational effectivity, prospering with much less time spent worrying about their provide chain and extra time making the most of alternatives for innovation.
The submit 3 Supply Chain Strategies for Manufacturers to Manage Rising Costs, Improve Visibility, and Boost Quality appeared first on Aberdeen Strategy & Research.
Source link